بررسی جامع جوشکاری پلاسما (PAW)
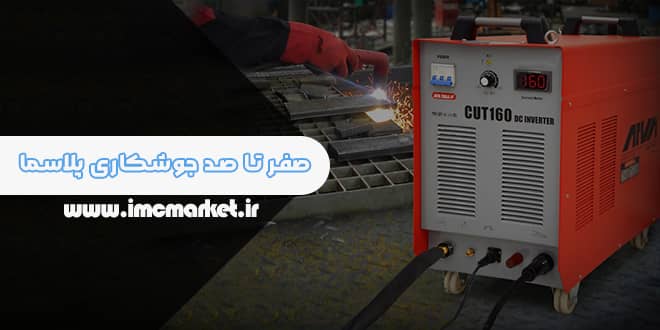
حدودا در تمام صنعتهای دنیا انواع جوشکاری کاربرد فراوان دارند. ویژگی مشترک آنها استفاده از حرارت حاصل شده از جریان قوس الکتریکی به منظور ذوب و اتصال قطعات فلزی است. همواره دقت و کیفیت جوش یکی از پارامترهای مهم انتخاب روش مناسب بر اساس نوع کاربرد مورد نظر است. شناخت روشهای مختلف و مزیتها و معایب آنها کمک شایانی به تشخیص نوع مناسب آن میکند. در این مقاله قصد داریم یکی از دقیقترین و با کیفیتترین روشهای جوشکاری یعنی جوشکاری پلاسما را معرفی کنیم.
پلاسما چیست؟
پلاسما یک گاز یونیزه شده حاوی تعداد تقریبا یکسانی از ذرات باردار مثبت و منفی است. از آنجایی که خصوصیات پلاسماها به طرز قابل توجهی از گازهای خنثی متفاوت است، به آنها حالت چهارم ماده میگویند. پلاسما از حرارت دادن بسیار زیاد گاز به گونهای که خاصیت رسانایی آن به شدت افزایش یابد حاصل میشود. در جوشکاری، پلاسما جهت سهولت عبور جریان قوس الکتریکی کاربرد دارد.
جوشکاری پلاسما (PAW) چیست؟
جوشکاری پلاسمایی نوعی از جوشکاری قوس الکتریکی است که طی آن یک قوس پلاسما بین الکترود و قطعه کاری شکل میگیرد. در نتیجه این کار، تمرکز حرارتی زیادی ایجاد شده و خط جوش نازک با عمق زیاد و پهنای کم ایجاد میشود. در این حالت قابلیت هدایت قوس الکتریکی بسیار بالا بوده، نفوذ بسیار بهتری درون قطعه صورت گرفته و پاشیدگی کمتری اتفاق میافتد. مصرف کم الکترود موجب افزایش دقت آن شده و امکان استفاده طولانی مدت را فراهم میکند. اگرچه هزینه این روش بسیار بالاست اما هزینه راه اندازی آن پایین بوده و یکی از بهترین روشها برای جوشکاری اتوماتیک به شمار میرود.
نحوه انجام جوشکاری پلاسما
هنگامی که دستگاه روشن میشود، برق وارد الکترود شده، جریان قوس الکتریکی ایجاد شده بین الکترود و قطعه کاری و همینطور الکترود و نازل خروجی موجب یونیزه شدن گاز آرگون اطراف الکترود و شکل گیری یونهای مثبت و منفی شده و یک جریان پلاسما تشکیل میشود. همزمان گازهای حفاظتی (ترکیب آرگون و هیدروژن) برای حفاظت از چشمه جوش تزریق شده و از آب برای خنک کاری نواحی درون سرپیک استفاده میگردد.
این نوع جوشکاری شباهت زیادی به جوشکاری تنگستنی دارد. در هردو از جریان قوس الکتریکی برآمده از الکترود تنگستنی مصرف نشدنی جهت ایجاد حرارت و ذوب قطعه کاری و از میله پرکننده برای پرکردن خط جوش و گاز های محافظ برای حفاظت از چشمه جوش استفاده میگردد. منبع تغذیه در حالت کلی جریان مستقیم بوده و برای آلومینیم و آلیاژهای آن میتواند جریان متناوب باشد. ولتاژ باید یک مدار باز ۸۰ ولتی بوده و دوره کاری (نسبت زمان کار به زمان کل) آن باید ۶۰ درصد باشد.
بهتر است یک سیستم کنترل ولتاژ و جریان به کار گرفته شود تا شدت جریان را در طول عملیات ثابت نگه دارد. در غیر این صورت افزایش بیش از حد شدت جریان به الکترود آسیب میزند. یک سیستم کنترل هم برای تنظیم دبی جریان گازهای ورودی مورد نیاز است. ترجیحا باید کنتاکتور هم به کار گرفته شده و قابلیت کنترل جریان از راه دور میسر باشد.
برای مواد نازک شده جریان ۲ آمپر کافی بوده و برای مواد ضخیم این مقدار تا ۳۰۰ آمپر هم پیش میرود. اینورترهای فرکانس بالا برای شروع عملیات به کار گرفته میشوند. همانند سایر روشهای جوشکاری، هم حالت دستی هم اتوماتیک برای این روش موجود هستند.
تفاوتهای جوشکاری پلاسما (PAW) با جوشکاری آرگون (TIG)
تفاوت عمده این دو روش این است که در جوشکاری تنگستن (جوش آرگون) نوک الکترود بیرون از سرپیک جوش قرار دارد در حالی که در جوشکاری پلاسما درون بدنه سرپیک قرار میگیرد تا بدین ترتیب گازهای ورودی تماس بیشتری با قوس الکتریکی ایجاد شده داشته و یونیزه شده و جریان پلاسما از بین این گازها تشکیل میگردد. همچنین برای جوشکاری پلاسما حتما باید یک نازل بر روی دهانه خروجی سرپیک جوش به منظور پایدار کردن و جهت دادن به جریان پلاسما قرار داده شود.
در این حالت دمای گاز به ۵۰ هزار درجه سانتیگراد میرسد. در حالی که در مورد جوشکاری تنگستن این مقدار در حد ۵ هزار درجه است. بدین ترتیب با دمای بسیار بالاتر سرعت جوشکاری و نفوذ آن بسیار افزایش یافته که موجب جذابیت این روش برای بسیاری از کاربردهای صنعتی میشود. لازم به ذکر است که علی رغم جوشکاری تنگستن، در جوشکاری پلاسما استفاده از آب خنک کننده حتی برای آمپراژهای پایین الزامیست چرا که حرارت تولید شده به حدی زیاد است که میتواند به ذوب شدن نازل بیانجامد.
یک ویژگی خاص جوشکاری پلاسما نسبت به جوشکاری تنگستن و انواع دیگر جوشکاری قوس الکتریکی این است که از دو ورودی گاز استفاد میشود. ورودی اول برای شکل گیری پلاسما بوده که دورتادور الکترود تنگستنی و در مرکز سطح مقطع سرپیک جوش قرار دارد. ورودی دوم که به عنوان گاز حفاظتی عمل میکند، پیرامون سطح مقطع سرپیک بین دیواره بیرونی و داخلی قرار دارد و مسیر آن از گاز اطراف الکترود به وسیله دیواره داخلی جدا شده است.
ویژگی ممتاز دیگر این روش جوشکاری مربوط به دوگانه بودن منبع حرارتی آن است. حرارت لازم برای ذوب کردن و جوش دادن قطعات از دو منبع یکی از قوس الکتریکی شکل گرفته میان الکترود و قطعه کاری و دیگری از طریق جریان قوس الکتریکی بین الکترود و نازل خروجی است. به همین خاطر است که حرارت بسیار شدیدی روی قطعه وارد میشود. به طور کلی نسبت عمق به عرض جوش در جوشکاری پلاسمایی بیشتر بوده و خط جوش آن عمیقتر و پرنفوذتر اما نازکتر است.
مزیتهای جوشکاری پلاسما
مزیتهای جوشکاری پلاسما نسبت به جوشکاری تنگستن مربوط به تمرکز انرژی بیشتر جوشکاری پلاسمایی است. به دلیل دمای بیشتر، سرعت بالای جت (خط باریک) پلاسما، گرمای بیشتری روی قطعه کار منتقل میشود. مزیت دیگر روش پلاسمایی در رابطه با مستقیم و پایدار بودن پلاسما بوده که به نسبت قوس الکتریکی جوشکاری تنگستنی دچار انحراف و زبانه کشیدن لحظه به لحظه نمیشود و دقت کار را بالا میبرد.
در جوشکاری پلاسمایی، فاصله بین الکترود و قطعه کاری بیشتر است. لذا جوشکار نظارت، کنترل و آزادی عمل بهتری حین کار دارد. همچنین به دلیل تمرکز گرمایی بالای جت پلاسما امکان جوشکاری سریعتر فراهم میشود.
یکی از مشکلاتی که جوشکاری تنگستنی دارد مسئله اعوجاج است. در بسیاری موارد قطعه کاری پس از اتمام جوشکاری و سرد شدن فلز جوش تاب برداشته و تغییر شکل میدهد. در جوشکاری پلاسمایی با تکنیکی که به آن اثر حفره کلیدی میگویند، این مشکل مرتفع میشود.
از آنجایی که قوس پلاسما باریک، متمرکز و دارای حرارت زیاد است، جوشکار میتواند در نقطه ابتدایی جوش، سرپیک جوش را بدون استفاده از میله پرکننده برای مدت بیشتری نسبت به بقیه نواحی خط جوش نگه داشته تا عمق بیشتری را ذوب کرده تا حفره درون قطعه شکل بگیرد. سپس برای باقی کار طبق روال معمول پیش برود. بدین ترتیب احتمال بروز اعوجاج بسیار کمتر میگردد. به این پدیده اثر حفره کلیدی گفته میشود. این تکنیک برای جوشکاری قطعات زاویه دار بسیار مفید است.
معایب جوش پلاسما
معایب جوشکاری پلاسما بیشتر مربوط به هزینه بالاتر تجهیزات آن از جمله نازلی است که لازم است روی دهانه سرپیک جوش نصب گردد. برای طراحی و ساخت این نازل و اریفیس (سوراخهایی که برای کاهش فشار سیال و ایجاد تعادل در آن استفاده میگردد) موجود روی آن باید ظرافت زیادی به کار گرفته شود. علاوه بر آن، به دلیل حرارت زیادی که تولید میشود، سیستم خنک کاری آبی ویژهای مورد نیاز است که متعاقبا موجب افزایش هزینه میشود. علاوه بر آن جوشکار مهارت بیشتری باید داشته باشد تا بتواند انرژی زیاد پلاسما را مدیریت و کنترل کند.
این روش دارای خط جوش نازک و پهنای کم بوده و پس از یک مرتبه جوشکاری ناهمگونیهای هندسی در برخی قطعات را ترمیم نکرده و نیاز به جوشکاری مجدد و هزینه کرد بیشتر دارد. به این دلیل است که در بسیاری از کاربردها که عمق کم و پهنای زیاد مد نظر است یا مواردی که دقت و عمق بالا چندان اهمیتی نداشته ولزومی به پرداخت هزینه سنگین جوشکاری پلاسما نیست مانند ساخت لولههای آکاردئونی، جوشکاران اغلب روش تنگستنی را ترجیح میدهند تا با هزینه کمتر بتوانند کار مطلوب خود را اجرا کنند.
کاربرد جوشکاری (PAW)
از آنجایی که سرپیک جوش به گونه ای ساخته شده که میتوان مقدار جریان گاز، شدت جریان برق و سایز نازل را به تناسب کاربرد مورد نظر تغییر داد، جوشکاری پلاسمایی کاربردهای بسیار وسیعی میتواند داشته باشد. از جوشکاریهای کم عمق برای مواد نازک تا جوشکاریهای عمیق برای مواد ضخیم و برای جنسهای مختلف مواد قابل اجراست. اما عمده کاربرد جوشکاری پلاسما در ساخت لولههای فولادی لکه ناپذیر و آلیاژ تیتانیوم با کیفیت بالا است که در صنایع مختلف از جمله نفت، شیمی و هوایی و فضایی کاربرد دارند.
با این روش سرعت کار و نرخ تولید لوله بالاتر از روشهای دیگر بوده و بهره وری تولید را افزایش میدهد. به دلیل تمرکز انرژی زیاد از این روش بیشتر برای آمپراژهایی پایین (۱۰۰ آمپر و کمتر) که برای مواد ضخیم کاربرد دارد استفاده میشود. از طرف دیگر به دلیل باریک بودن جت پلاسما، برای جوشکاری قطعات کوچک مانند اتصالات لب به لب که ظرافت بالایی مد نظر است کاربرد دارد.
جمع بندی
در این مقاله به شرح پلاسما و کاربرد آن در جوشکاری ، بیان مزایا و معایب آن و مقایسه آن با جوشکاری تنگستنی پرداخته شد. هر قطعه ای که توسط جوشکاری تنگستنی قابل جوش است، برای جوشکاری پلاسمایی هم قابل اجرا خواهد بود. جوشکاری پلاسما برای جوشکاری انواع مختلف مواد با جنس ها و ضخامت های مختلف کارایی دارد. همیشه دقت و کیفیت جوش آن از نوع تنگستنی بیشتر است ولی در برخی موارد به لحاظ اقتصادی به صرفه است و در برخی موارد نیست.
همانگونه که اشاره شد. به طور کلی جوشکاری پلاسمایی نسبت عمق به پهنای آن بیشتر است. نفوذ بیشتری درون ماده داشته اما پهنای خط جوش آن نازک است. بسته به نوع کاربرد، برخی موارد جوشکاران برای اولین دور از جوشکاری پلاسما استفاده میکنند تا یک جوش محکم و دقیق اما نازک ایجاد شود. سپس برای دور دوم از جوشکاری تنگستن استفاده میکنند تا یک خط جوش پهن ایجاد شده و تمام سطوح قطعه را پوشش دهد. البته جریان پلاسما برای برش هم به کار میرود که از موضوع این مقاله خارج است.
اگرچه فهم عمیقتر موضوع نیاز به مطالعه و تجربیات بسیاری دارد، آروا تولید کننده انواع اینورتر جوشکاری و ابزار آلات صنعتی و خانگی امیدوار است با مطالعه این مقاله خواننده به درک روشنی از موضوع رسیده و برای وی مفید فایده باشد.
اولین دیدگاه را ثبت کنید